Services
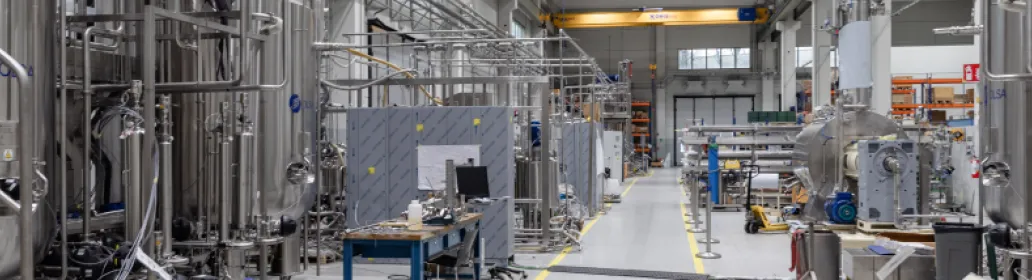
We’d love to talk to you about after sales service needs
Need spares?
We know that spare parts management plays a critical role in operations, as it directly influences the lifespan and uninterrupted operation of a water production system.
For this reason our Spare Parts department is closely integrated with our After Sales services, ensuring optimal synergy between the two departments. This approach allows us to offer comprehensive solutions to tackle any potential critical situations on-site, ultimately prioritising the best interest of customers.
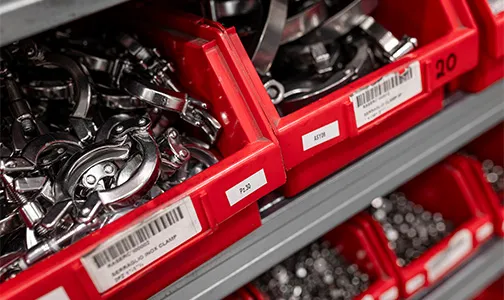
We provide:
Recommended spare parts list
Leveraging its vast experience with thousands of plants operating worldwide, Stilmas can provide a minimum package of critical spares that should be kept at the Customer's site. These spare parts serve for periodical preventive maintenance and can be utilised in case of a component failure.
Emergency spares kit
To ensure prompt support, Stilmas maintains a stock of critical spare parts. This selection is based on a statistical study that identifies the most common criticalities.
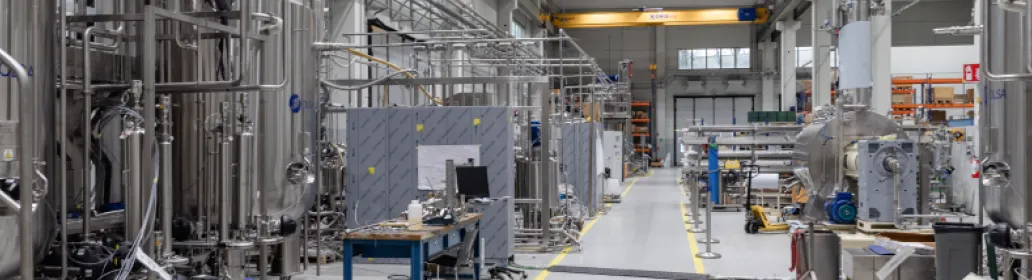